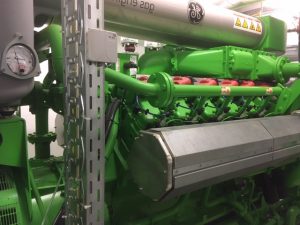
Gasmotor im Betrieb in Raumaufstellung
Ganztages-Seminare zum Thema “Optimaler BHKW-Betrieb” stießen in jüngster Zeit auf großes Interesse der Betreiber. Oft wurden auch auf Wunsch die Themen ergänzt, die beim Flex-Betrieb zu beachten sind.
In den Veranstaltungen stellte sich heraus, dass die Interpretation der Betriebsdaten oft Schwierigkeiten bereitet. Damit fehlen wichtige Informationen, um die Schadenprävention zu unterstützen. Mit den täglich erfassten Betriebsdaten des BHKWs hätte der Betreiber die Chance, frühzeitig gemeinsam mit dem Servicepartner vorbeugend einzugreifen.
Es geht dabei um Gefahren erhöhter Temperaturen in den Kühlkreisläufen und in der Gemischversorgung, die den Betreiber bei Nichtbeachtung viel Geld und ungeplante Stillstände kosten. Beispielhaft seien 6 Einflussfaktoren angesprochen, die in der Praxis immer wieder zu teuren Störungen führen.
1. Betriebstemperaturen in Kühlkreisläufen zu hoch
Hohe Kühlwassertemperaturen führen zu vorzeitiger Materialermüdung im Bereich der Zylinderköpfe, Laufbuchsen und Zündkerzen. Diese Bauteile erreichen früher ihre Verschleißmaße und erhöhen somit die Betriebskosten. Die Standzeiten dieser Bauteile sind bei den gleichen Motortypen sehr unterschiedlich und weisen auf die unterschiedlichen Arbeitsumgebungen der Motoren hin. Darauf hat schon der Anlagen-Planer und Projektierer einen großen Einfluss. Liefert die Inbetriebnahme des Aggregates keine Betriebstemperaturen im Sollbereich, sind die Wurzeln für vorzeitigen Verschleiß gelegt.
Es gibt mehrere Ursachen für zu hohe Betriebstemperaturen in Kühlkreisläufen, die auch in der zunehmenden Verschmutzung der Wärmetauscher liegen. Deshalb sind die Temperaturänderung der Kühlmedien wichtige Indikatoren für anstehende Reinigungsarbeiten an Wärmetauschern und Notkühlern.
2. Schmieröltemperatur im BHKW-Betrieb zu hoch
Schmieröl kann eine Menge Temperatuerhöhung ertragen, bevor der Schmierfilm reisst. Aber weit davor sind wichtige Additive schon zerstört. Und die Schmierölanalyse zeigt hohe Oxidationswerte, die einen vorzeitigen Schmiereölwechsel erfordern. Die Schmieröltemperatur zeigt ein Sympton an (im Motor herrschen zu hohe Temperaturen) und wirkt selbst auf die zu schmierenden Bauteile mit weniger Leistung als Schmieröl (Additive zerstört) ein.
Auch hier gibt es ein Ursachenbündel, das vom verschlammten Ölkühler bis zur klopfenden Verbrennung des Motors reicht. Oft wirken auch mehrere Ursachen gleichzeitig und erfordern daher eine saubere Auswertung der Motor-Betriebsdaten. Wer zu früh mit der Fehlersuche aufhört, wundert sich dann, dass die Temperatur immer noch zu hoch ist.
3. Hohe Gemischtemperatur führt zur Leistungsreduktion oder zum Totalschaden
Gute Motorsteuerungen schützen den Motor vor zu heißem Gemisch und reduzieren die Motorleistung. Bis die Gemischtemperatur wieder ein erträgliches Temperaturniveau erreicht hat. Wer keine Sensorik hierfür hat, läuft Gefahr, dass zu hohe Brennraum-Temperaturen und -Drücke den Motor massiv schädigen. Dies reicht dann bis zum einzelnen oder gemeinschaftlichen Kolbenfresser und Lagerversagen.
4. Ölnebeldämpfe im Brennraum
Der verborgene Champion mit starker Zerstörungskraft im Motor sind Ölnebeldämpfe. Als starke Brandbeschleuniger führen sie ausnahmslos zu massiven Motorschäden. Den Zustand der Ölnebeldampfabscheidung sauber im Auge zu behalten, ist daher eine wichtige Aufgabe im BHKW-Betrieb. Überhaupt hat Schmieröl nichts im Ansaugtrakt zu suchen, kommt es nun von undichten Turboladern oder von verschlissenen Einlassventilführungen.
Je nach Menge des in den Brennraum eingetragenen Schmieröles werden auch Bauteile im Abgastrakt durch harte Beläge und Ölkohleaufbau geschädigt, wie z.B. der Abgasturbolader.
5. Kondensatabführung
Gerade im Winterhalbjahr ist die Gefahr der Kondensatbildung in der Biogasleitung groß. Wenn durch unzureichende Erwärmung oder Rohrisolierung die Feuchtigkeit im Biogas ausfällt, bekommt im schlimmsten Fall der Motor durch die Wassermenge Schluckbeschwerden. Überdies hinaus erhalten die Komponenten wie Nulldruckregler oder Gemischregler mit dem Kondensat auch Schmutzpartikel, die sich in den empfindlichen Bauteilen ablagern und zu Störungen führen.
Freie Kondensatschächte und regelmäßige Entleerung der Kondensatabzüge von Abgaswärmetauschern sind wichtige Programmpunkte im BHKW-Betrieb, da anderenfalls dort auch große Korrosionsgefahr droht.
6. Biogasaufbereitung im BHKW-Betrieb oft vernachlässigt
Die Qualität der Biogasaufbereitung steht und fällt mit dem Fahren im optimalen Bereich der Aktivkohle. Im Seminar “Optimaler BHKW-Betrieb” wird genau erläutert, welche Bestandteile (u.a. Sauerstoffgehalt) und Zustandsgrößen (Feuchte und Temperatur) zu einer optimalen Beladungsleistung der eingesetzten Aktivkohle führen. Für Schwefelwasserstoff gilt eine Null-Toleranz-Politik, um Lagerschäden, versauerndes Schmieröl und korrodierte Abgaswärmetauscher zu vermeiden. Die penible Überwachung wird mit höherer Verfügbarkeit des Aggregates und geringeren Betriebskosten (insbesondere Instandhaltung und Ausfallkosten) belohnt.
Technische Betriebsführung erfordert Hand am Puls des Biogasmotors
Die im BHKW-Betrieb gewonnenen Motor-Betriebsdaten geben klare Signale, was für einen weiteren störungsfreien Betrieb zu tun ist. Entweder für den Betreiber selbst oder den involvierten Service-Betrieb. Es gäbe also gute Chancen, die heute noch sehr unterschiedlich hohen Ausfallzeiten und Instandhaltungskosten auf ein günstiges Maß zu reduzieren. Wenn Betreiber und Servicepartner die kontinuierlich gemessenen Daten bewerten und dann rechtzeitig (nicht zu früh oder zu spät) gegensteuern.
Häufig sind es die kleinen Stellschrauben, die oft Wunder wirken und den Alltagsstress mit dem BHKW deutlich reduzieren. Wir unterstützen Betreiber hierin, z.B. mit den schon oben angesprochenen Seminaren, die insbesondere auch für den Flex-Betrieb wichtige Hinweise enthalten. Aktuelle Termine sind hier für Nienburg und Freiberg verlinkt.