Noch sind die Außentemperaturen so tief, dass Motoren eigentlich keine thermischen Probleme haben sollten. Die Praxis vor Ort spricht dagegen in vielen Fällen eine andere Sprache. Wenn zu dieser Jahreszeit Motoren schon an den Grenzwerten für Kühlmittel- und Gemischtemperaturen kratzen, lohnt es sich, auf die Ursachen zu schauen. Die Motorkühlung hängt von mehreren Faktoren ab:
- Zustand der Wärmetauscher
- Raumluftwechsel
- Zustand des Kühlmittels
- Parametrierung der Regelventile
- Zustand des Schmierölkühlers
- Kühlmitteldrücke in den Kühlkreisläufen
- Luftseitige und wasserseitige Kühlflächen der Notkühler
Gute Motorkühlung reduziert den Verschleiß
Hochbelastete Biogasmotoren beanspruchen Zylinderköpfe und Zündkerzen sowie Laufbuchsen, Kolben und Kolbenringe. Häufig kühlen Ölspritzdüsen die Kolbenbodenunterseiten. So leistet das Schmieröl auch seinen Beitrag zur Motorkühlung und führt diese Wärme über den Schmierölkühler an den Motorkühlkreislauf ab. Manche Motoren koppeln die Schmierölwärme auch direkt aus und machen die Wärme für Heizwärme direkt nutzbar. Ein ausreichend großer Schmierölkühler, der regelmäßig gereinigt wird, ist dann auch ein Garant für Schmieröltemperaturen, die den Additiven eine lange Standzeit ermöglichen. Temperaturen um 100°C und mehr zeigen eine hohe thermische Belastung an, die die Additive rasch “in die Knie gehen” lassen.
Die Standzeiten von Zylinderköpfen und Zündkerzen hängen direkt von ihren Betriebstemperaturen ab. Je tiefer diese sind, desto geringere thermische Belastungen wirken als verschleißfördernder Stress auf diese Bauteile.
Niedriger Kühlmitteldruck als Schadenstreiber
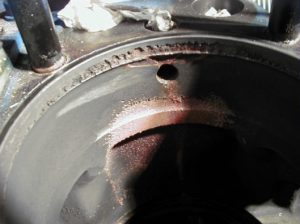
Materialabtrag durch Kavitation im Kühlkreislauf
Die Kühlmitteldrücke bewegen sich unterhalb des Radars vieler Betreiber. Solange noch Kühlmittel im Kühlkreislauf ist, scheint alles in Ordnung. Für die Motorkühlung ist auch ein ausreichender Kühlmitteldruck sehr wichtig, da sich anderenfalls Dampfblasen bilden, die nicht kühlen. Und die unangenehme Eigenschaft haben, Material von Laufbuchsen und vom Motorblock wegzufressen: Kavitation bedingt durch implodierende Dampfblasen führt so zu teuren Motorschäden.
Kühlmitteldrücke von einem bar und weniger sind absolut zu gering. Mindestens 1,5 bis 2,5 bar geben erst den Schutz vor unerwünschter Dampfblasenbildung. Die Kühlmitteldrücke sind in den Kühlkreisläufen nicht überall gleich hoch, aufgrund der Strömung des Kühlmittels und der Strömungswiderstände durch Ventile oder enge Radien gibt es nämlich Druckabfälle, die den am Manometer angezeigten Druck deutlich reduzieren können.
Kühlmittel sind keine Lebensdauerfüllung für Motoren
Schmierölwechsel stehen viel stärker im Bewustsein von BHKW-Betreibern als Kühlmittelwechsel, da deren Wechselintervalle ja auch wesentlich kürzer sind. Trotzdem sollte man dem Kühlmittel die Aufmerksamkeit im Rahmen der Instandhaltung schenken, die es für eine gute Funktion benötigt. Das heißt, eine jährlich Überprüfung und Anlyse einer Kühlmittelprobe ist kein Luxus, sondern wirksamer Schutz, um die Leistungsfähigkeit der Motorkühlung zu erhalten.
Ein Beispiel einer Kühlmittelanalyse erhalten Sie über diesen Link. Der Aufbau ähnelt einer Schmierölanalyse und gibt dem Servicepartner wie auch dem Betreiber ein zutreffendes Bild über den Verschleißzustand des Kühlmittels und besondere Belastungen aus dem Einsatz im Kühlktreislauf.
Motor als Wärmequelle unterschätzt
Die Strahlungswärme des Motors – bei einem 500 kW-Motor immerhin ca. 95 kW – heizt den Betriebsraum auf und führt zum Ansteigen der Raumlufttemperatur. Steigt die Temperatur über 35°C wird es nicht nur dem Service- und Bedienpersonal zu warm, sondern auch dem Motor. Es droht dann nämlich ein Anstieg der Gemischtemperatur in Richtung Klopfgefahr. Dies bedeutet für den Gemischkühlkreislauf harte Arbeit, um die Gemischtemperatur in gesunden Grenzen zu halten.
Die Strahlungswärme lässt sich nur wenig reduzieren, indem abgasführende Teile wie Sammelrohre und Abgasturbolader wärmeisoliert oder wassergekühlt werden. Ein Grund mehr also auf eine gute Fitness der Motorkühlung zu achten. Damit wird ein wichtiger Beitrag geleistet, die Kondition des Biogasmotors zu verbessern und vorzeitigem Verschleiß vorzubeugen.